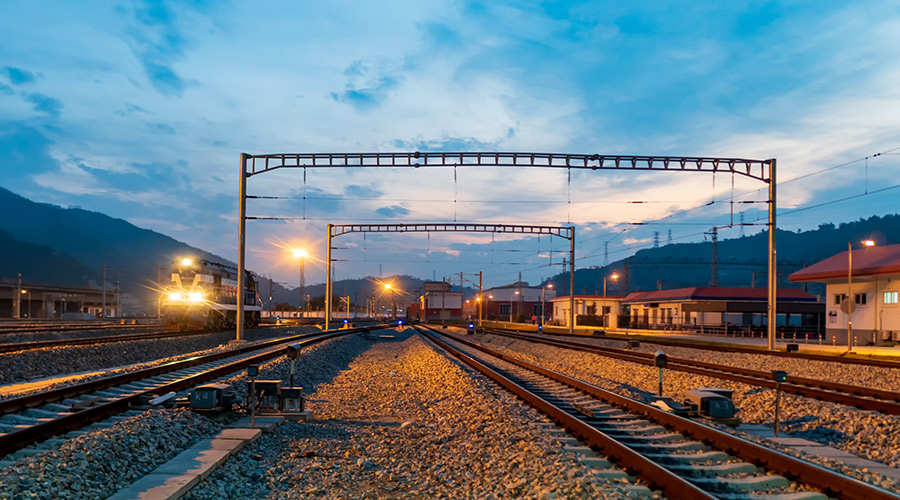
There is a famous city in the southwest of Shandong Province. Confucius, a great thinker, educator and founder of Confucian school in ancient China, was born here. This city has had a profound impact on China, Asia and even the world. It is the holy city of the east and the hometown of Confucius-Qufu.
As one of the important birthplaces of Chinese civilization, Qufu has been a treasure of ancient China and a land of outstanding people. There have been countless gifted scholars, celebrities and well-known entrepreneurs with Confucian temperament. It is the source of world-famous Confucianism and the root of Confucianism. With the development of history, many representatives of Confucian businessmen have emerged in Qufu. They not only inherited the spiritual connotation of Confucian culture, but also took a new step in scientific and technological innovation.
Qufu Juli Railway Track Engineering Co., Ltd. is one of them.
The company formerly known as Qufu City Juli Steel Mold Steel Structure Co., Ltd. is located at the southern end of Chuangye Avenue, Taiwan Industrial Park, Qufu Economic Development Zone. It is adjacent to the Beijing-Shanghai Expressway in the east, the Ridong Expressway in the south, the Beijing-Fuzhou Expressway in the west, and the intersection of National Roads 104 and 327 in the north. It has advantageous geographical location and convenient transportation. Since its establishment in 2001, the company has been committed to producing high-quality ordinary crosstie, high-speed crosstie, subway crosstie, support fast crosstie, light rail crosstie steel molds and non-standard production equipment. Electrified overhead lines pillar production line and steel mold; spherical hinges, sound barriers and various concrete components; isolation construction prodcuts
After more than ten years of development, Juli has developed into a plant with an area of more than 200 acres, a construction area of more than 30,000 square meters, and more than 350 sets (sets) of various mechanical power equipment. The total value of fixed assets reached more than 80 million yuan.
In order to continuously improve the company's management and business level, the company has continuously restructured and optimized its personnel structure. Not only has it set up a five-department management system under the top management of the chairman, general manager, deputy general manager and chief engineer, but it has also built a professional and technical team of over 100 people. Among them, there are 7 with senior technical titles, 31 with intermediate technical titles, 18 with primary technical titles and 48 with professional and technical workers.
With the help of talent introduction, capital investment and innovation and research and development of technical products, all kinds of railway track products produced by the company have won the recognition of the vast number of users in the field of railway track design. Juli Company was designated as the product experimental production base by the professional design institute of the Ministry of Railways in 2002. Together with the Ministry of Railways, we have developed railway track molds and new models at speeds of 120, 200, 250, 300, and 350 kilometers per hour. These models have been unanimously praised by China Railway Group 1, 3, 8, 11, 12, 14, 14, 16, 19, 21, 23, 24, MBEC, CRTG, CNFC, CCECC.
High-quality products not only make Juli win the reputation of the industry, but also allow it to participate in the construction of many national key engineering projects.
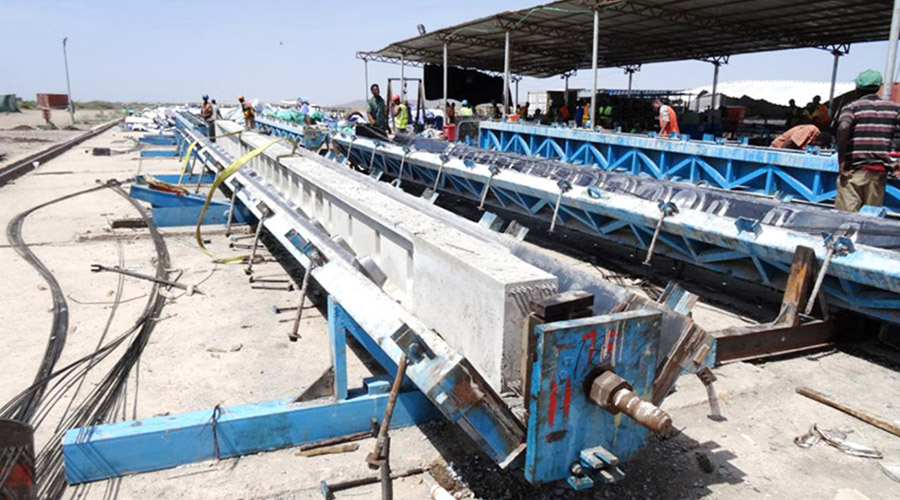
In order to meet the Beijing-Tianjin intercity high-speed rail project constructed in 2008 Olympic Games, Juli provided the technology and manpower for bridge steel molds in 2006.
In June 2014, in cooperation with CCECC, technicians were dispatched to Ethiopia to guide the installation of equipment and molds.
In February 2018, we cooperated with CCECC again, and appointed technicians to go to Nigeria to guide the installation of equipment and molds, and produced qualified products within a short period of time.
From domestic key projects such as Qinghai-Tibet Railway, Beijing-Shenyang Railway, Harbin-Dalian Railway, Beijing-Shanghai Central-South Passage, Jiaoji Railway and other well-known railway construction projects such as China's international support for railway construction in Asia and Africa, Juli Company has provided reliable technical guidance in the manufacture and installation of railway production lines and molds.
In the face of achievements, the company has not stopped the pace of technological innovation. In 2003, it passed the ISO9001 international quality system certification of Qufu Juli Steel Mold Steel Structure Co., Ltd. In 2013, it also cooperated with Beijing Jiaotong University to jointly develop the country's first RPC concrete ball joint, which won 17 national patents and was reviewed and approved by senior experts. In September 2015, it passed the "Qufu City Juli "Railway Engineering Co., Ltd." ISO9001 international quality system certification.
For better research and development and production of railway tracks, Juli Company has also jointly invested RMB 30 million with Beijing and Bengbu to establish Rongbang Transportation Rail Technology Co., Ltd. and establish an advanced domestic crosstie production line. At present, through R & D, the production lines and molds required by the UAE national project railway crosstie are produced. The company's products have reached the standard and have been sold to Beijing, Tianjin, Shijiazhuang and other countries as well as Ethiopia, Nigeria, UAE and other places. The products have been well received by customers at home and abroad. At present, the export of the products has greatly increased and the demand exceeds the supply.
In the past two decades, Qufu City Juli Railway Track Engineering Co., Ltd. inherited the spirit of Confucianism, operated with integrity, and constantly innovated. Not only has the quality of products been continuously improved, and the output value of enterprises has increased year after year, but it has also made an indelible contribution to China's rail construction business. It has become a well-known manufacturer of molds and non-standard equipment in the domestic railway industry. The employees of Juli are currently struggling to build a beautiful new Juli with full enthusiasm and new pursuit, concentrating their strengths, advancing with the times, pioneering and enterprising, breaking through innovation.
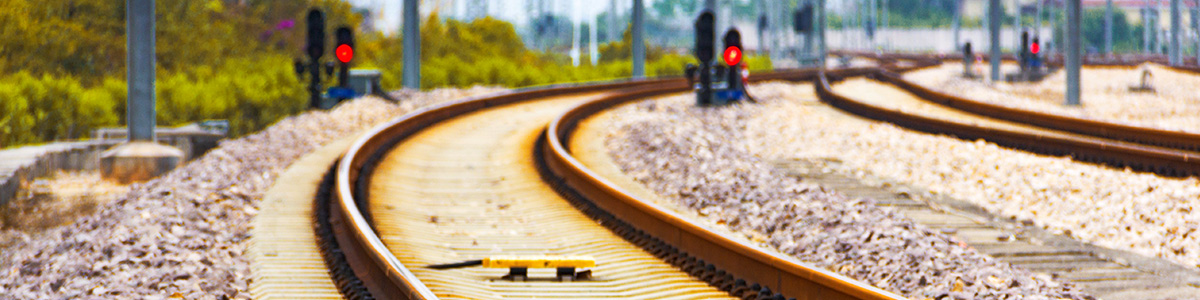
Animation demonstration of Juli railway track
production process
Mold clearing process:Clean up the concrete sludge or impurities on the end and both sides of the demoulded mold. ?The diluted isolating agent is sprayed from the spray head in fog and evenly sprayed on all parts of the surface of the steel mold.
Installation of embedded casing:By installing rubber bolts, high-performance resin bolts, iron bolts and other process accessories, 80-degree lateral formwork erection of the mold can be realized, which is convenient for fixing embedded parts. Fittings such as embedded casing shall be fixed firmly and vertically to prevent defects such as subsidence and inclination of finished casing.
Pre-stressed steel bar molding process:According to the arrangement position of crosstie steel wires, cut steel bars are inserted into corresponding tensioning plates and pulp blocking plates, and both ends are upset. Move the steel wire group with the upset head together with the tensioning plate and the slurry blocking plate into the steel mold. ?Stirrup and spiral steel bar are installed and placed at specified positions, tensioning plates at both ends are respectively inserted into tensioning boxes and mold fixing ends, and slurry blocking plates are fixed at both ends of each mold with rubber partition plates to tightly adhere the slurry blocking plates to the end surface of the mold to avoid slurry leakage.
Tensioning process:Tensioning force is automatically controlled and stored according to computer. First of all, use the tensioning nut to firmly connect the tensioning screw of the mold with the tensioning machine. ?Then, the tensioning program is started for automatic tensioning. ?When the initial tensioning force reaches about 60kN, quickly knock the tensioning plates at both ends of the mold to make the prestressed reinforcement reach the specified position. Then, start the second tensioning, and lock the nut while tensioning. ?When the tensioning force reaches the specified value, keep it for one minute while locking the tensioning nut. After the tensioning operation is completed, wait to enter the next process.
Concrete mixing process:According to the moisture content of sand and stone materials detected every day, the technology department will automatically control the concrete mix proportion by computer to realize the accurate weighing of raw materials, and the materials will be discharged after twice mixing. The mixed concrete mixture is discharged into the storage hopper of the pouring truck under the platform through the discharge door.
Perfusion process:First of all, the surface of the mold and the temperature of the concrete should be measured regularly every day, and the concrete should be poured after meeting the technological requirements. ?Perfusion is performed in two times. ?First, slowly open the bin door and spit it according to the ratio of 1/3. Second, the size of the opening of the hopper opening should be well controlled and the materials should be continuously discharged so as to make the materials spat in each part as appropriate and even as possible.
Concrete vibration process:The crosstie mold filled with concrete is smoothly transported to the vibration table through a mold feeding roller table. ?Start the process for vibration compaction, and then smoothly transport the crosstie mold to the next vibration table. Align the embossed cover plate with the mold position and cover tightly. ?Then, a certain period of loading vibration is carried out.
Clean edge and into kiln:First of all, clean up the excessive concrete on the mould sleeper groove and edges. Besides, the bottom must be set perfectly horizontal.After the flush process, the mould is conveyed to pool table with a vertical roller rail. For lifting the sleeper mould into the kiln, the sleeper mould must be placed down gently along the rail, to avoid any vibration. The mould in the kiln should be kept in order,vertically and horizontally. After the kiln is filled, cover the kiln completely. Remember to keep proper amount of water in the seal groove to prevent leakage, and notify the maintenance staff to perform maintenance.
Maintenance process:The sleeper is maintained with steam of automatic temperature control. The control technique should be in accordance with the specific season. The maintenance is divided into four stages: static, heating, constant temperature and cooling. The maintenance time should be determined according to the technical specification.
Release process:Releasing is carried out in two ways: automatic hydraulic releasing machine or hydraulic wrench. The automatic releasing machine is used to slowly release the stress, and the releasing force shall not exceed 90% of the tensioning force. Cut the steel wire until the stress is relaxed. It is absolutely forbidden to cut the steel wire directly under the condition of stress. After releasing, the crosstie will be sent to the demoulding machine.
Demoulding process:After the staff confirm that the sleeper mould is firmly stuck in the stripping arms, activate the stripping machine. The mould will be rotated for 180 degrees and then lightly falls on the product table. Then the sleeper will be conveyed to cutting machine for cutting. The cutting process requires a friction saw for slow cutting. The gap must be aligned to the saw to prevent damage. During this period, the full-time inspector shall conduct inspection according to the product qualification standard, so that the qualified products and unqualified products are stored separately.
Stacking process:After cutting, the sleepers should be stacked. The stacking should be neat, and a 5cm of hard wood piece should be placed on the outer side shoulder of the sleepers for each layer of stacking. The stack needs to be perfectly horizontal. During the stacking, the steel plate should be removed and cleaned, then returned to the working section of steel wire processing. The stacked sleepers are then conveyed to warehouse by vehicles. When stored, a wood stick of thickness no less than 4cm should be placed between each layers of sleepers to facilitate delivery. The inspected sleepers will then go through warehouse procedures with the certificate issued by QC department. Sleeper after storage, Late curing shall be carried out in accordance with the technical specifications.